Dana Demsky (BFA ‘17) on the BioFabricate 2015 Conference
Close your eyes. It is now 2079. The world has changed dramatically and biofabrication is our way of survival. Biofabrication is the only science that survived to reflect the changing environment and the only science that was shared as it was emerging — and now it has saved us all. This dark imagining of the future opened a BioFabricate 2015 talk by Rodrigo Martinez, Life Sciences Chief Strategist and Senior Portfolio Director of global design company IDEO.
As haunting as the talk was, it really got to the root of what the BioFabricate 2015 conference was all about: a place to share ideas and projects related to the evolving and budding (literally) field of biofabrication. Biofabricate is the future of science and art. I was lucky enough to witness the shaping of this future in October 2015 in New York City, thanks to the Irene Bendler Bychinsky Award in Design and support from Dean Guna Nadarajan.
So, what exactly does “biofabrication” mean? Basically, it is all about making consumer products that are designed and grown using biological organisms; in essence, it is a biological revolution in the material world. Biofabrication aims to be an innovation that creates a more sustainable future. The best way to really understand this blossoming world of bio products is to give you examples of my favorite work shown at the conference.
BioFab: Living Colors
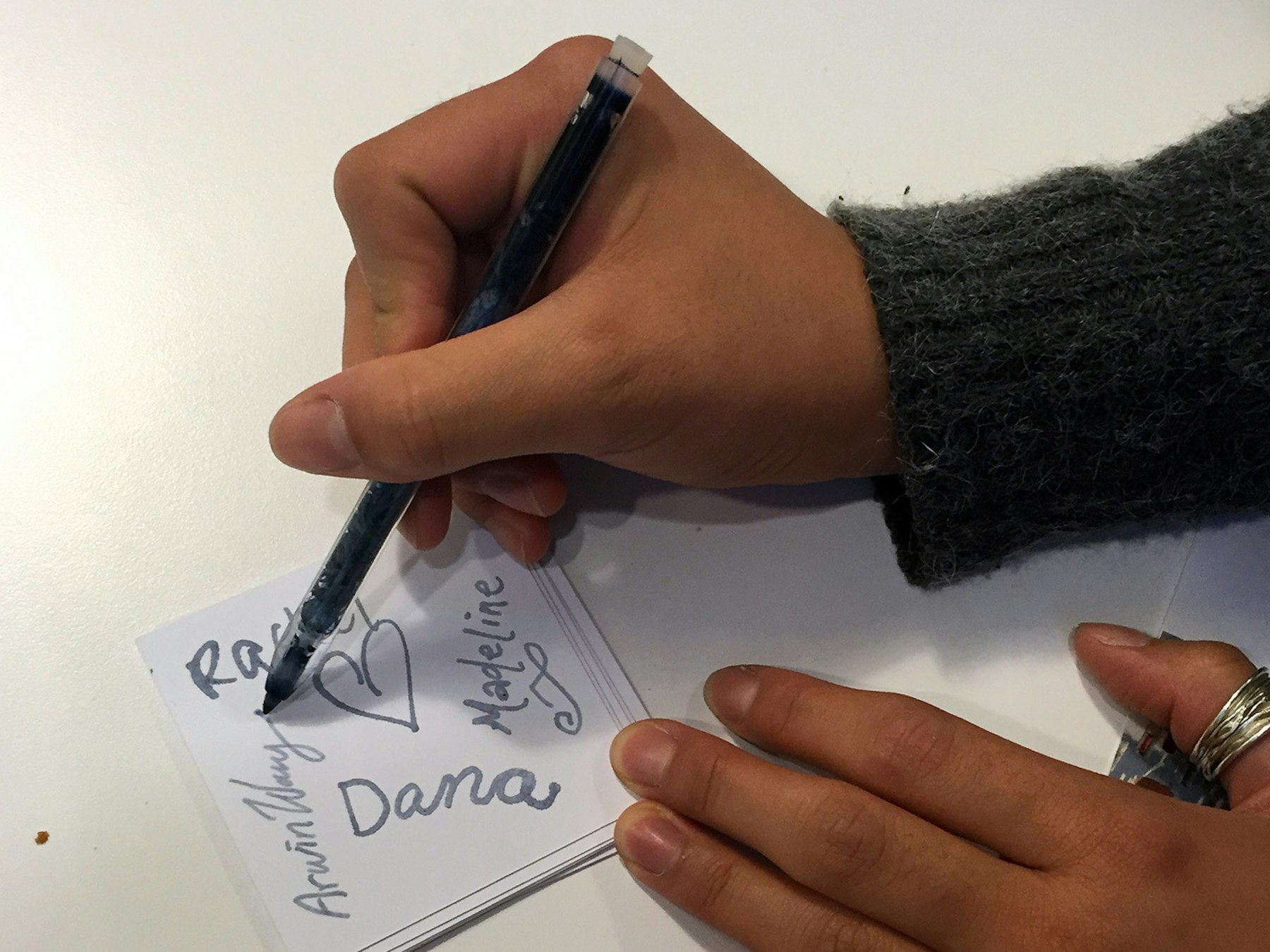
Think about this: we always say that color brings something to life, but now the colors are really living. How? Well, Thomas Landrain, co-founder and CEO of Pili Bio has figured it out. His company is working on engineering renewable dyes and pigments made from bacteria. The art applications here are incredible, from growing colors directly onto fibers to create unexpected patterns for textiles, to organic ink for printing. Pili Bio already has some bacteria ink for pens on the market, and they are working on creating printers that use the ink. Landrain said that they expect the first commercial bio-dyes to be ready in about six years. That seems like a long time, but there is so much biology and chemistry research that is going on behind the work that the six-year timeline is actually incredible. I got to try drawing with one of the bio living color pens and, I have to say, it worked pretty well!
BioFab: Negative Carbon Footprint
Now let’s switch from ink to the world of 3D sculpture and the attempt to make user products with a NEGATIVE carbon footprint. Impossible right now, but Eric Klarenbeek is striving to make this happen. Dubbed a “Designer of the Unusual,” Klarenbeek built a huge 3D printer that has a nozzle to deposit mycelium (a type of fungi). He uses this material to build furniture such as the stool that was shown at the conference. These structures dry after just a few days, and are stable from that point onward. The structures then continue to grow on their own, creating coral-looking growths. I think these grown-furniture pieces are beautiful, so unique and delicate. Even moving past aesthetics, it is incredible how these practical art forms are part of a grander mission to create zero waste and instead give back to the earth. Klarenbeek is continuing to work out how the entire process, from building the printers to transportation, can be waste-free.
BioFab: BioBots
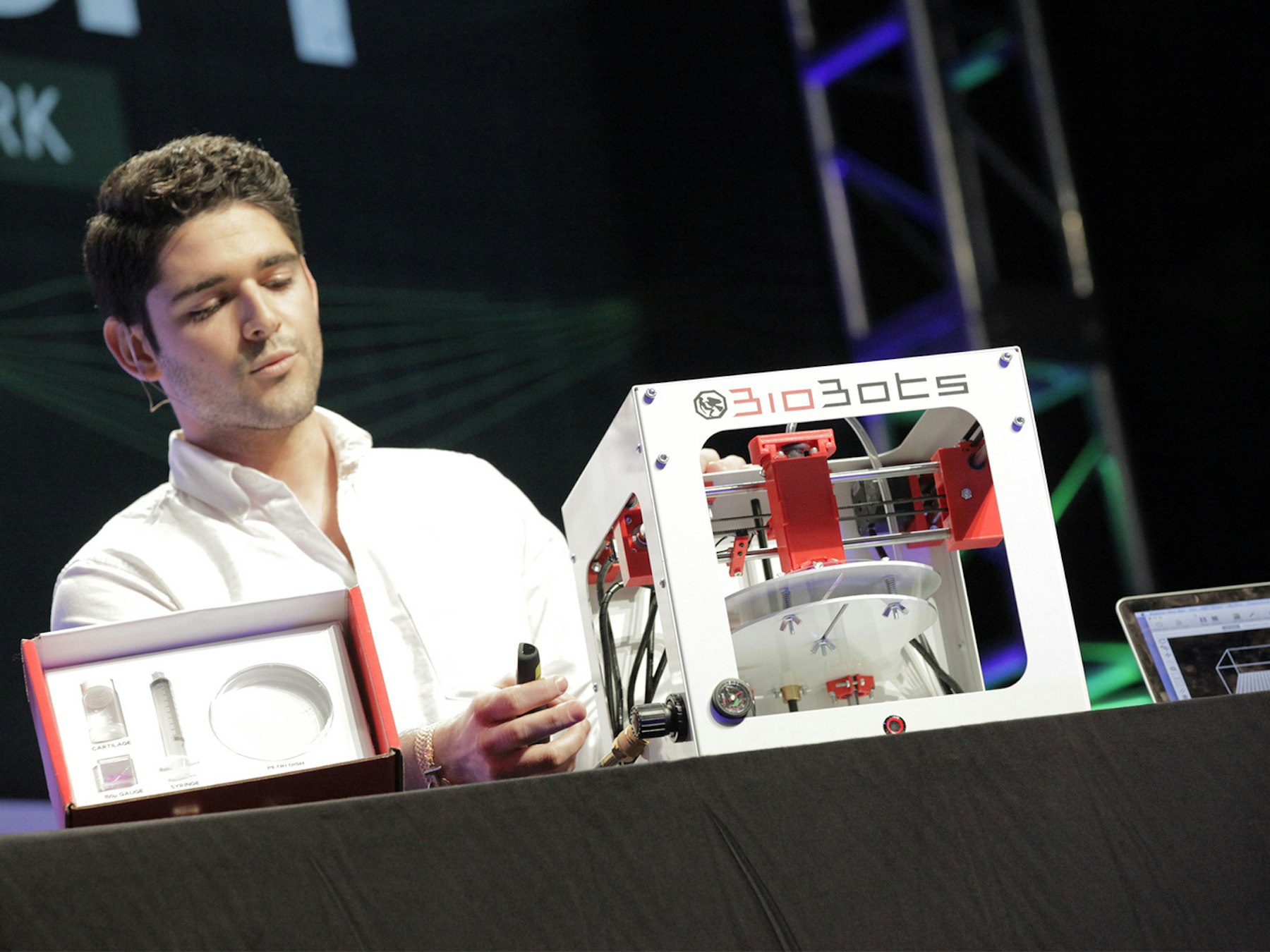
I now introduce you to Danny Cabrera, co-founder and CEO of BioBots, a 3D printer of entirely different size and purpose from Klarenbeek’s furniture builder. This small-cube-like printer is designed to print real, usable human body parts made up of real tissue. Cabrera and his team have run into obstacles to that goal: the cells can’t survive in the environment of the printer for the duration of the print. They are still working out how to create a more sterile interior so that the material can thrive. So far, the BioBot printer has successfully been used to model the inner human body for medical research, using material that is not real human tissue. BioBots just released a new 3D printer three weeks before the conference, and if this topic is sparking your interest, Cabrera said he’d be happy to sell one for the low price of $10,000! I might have to stop buying so much Bert’s coffee at Pierpont Union to save up for one of those…
BioFab: Reflections
It was an exhausting day in New York, but I came out of the conference with a new outlook on the possibilities for art. I realized that something I work on in the future might not even be invented yet. And that is truly astonishing. We are on the verge of new technology, and these innovations NEED artists. Artists are the creative minds that push technologies, like BioFab, to higher heights and to new applications. And it’s the designers that figure out how these technologies can be most easily used by the people who need it the most.
At Stamps, I am currently taking a digital fabrication class where we just finished a project working with 3D printers. For my project, I modeled a toy horse and printed her, but imagine what my horse could be in the future. With the BioBots’ technology, could I be printing a real mini pet pony in twenty years? The technology we know today has endless possibilities for the future.
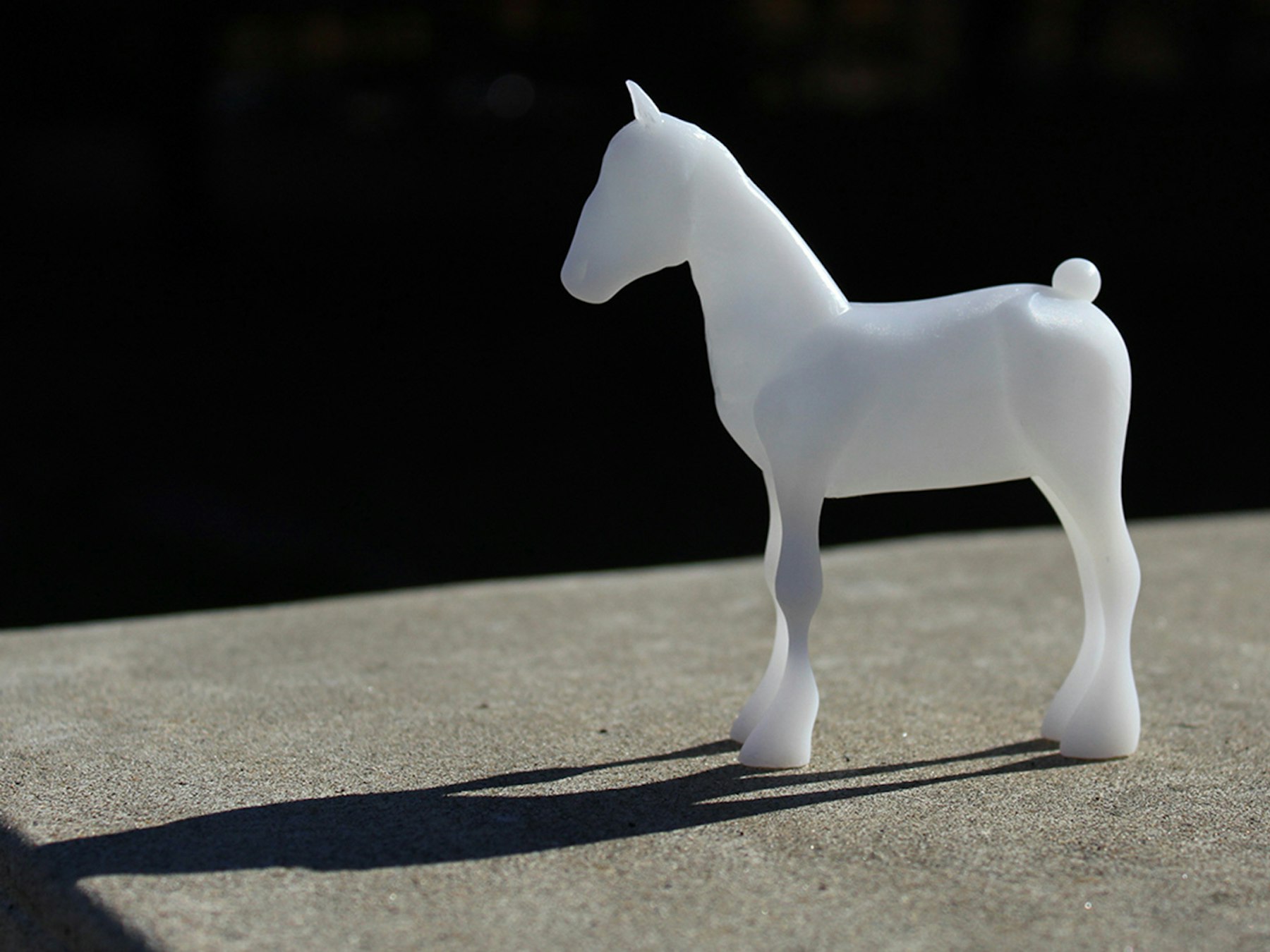
Living colors, organism-created stools, and 3D printed organs — this is just where biofabrication begins. There are so many more unimaginable inventions and creations coming that you won’t want to miss. Keep your eyes open, continue to be inspired, and watch out for biofab as it strives to grow the future.
Dana Demsky is an aspiring product and graphic designer at the Stamps School of Art & Design at the University of Michigan. She sees art as an endless journey of learning. Her work combines the practical ideology of design with her own personal passions. See Demsky’s work at danademsky.com.